Your customer asks for an overview of their current stock, can you present this information right away? or will your employees be spending at least a day counting the inventory? Or a priority order is required to be picked, but the inventory doesn’t seem to add up – what do you do then?
Nowadays if you’re not keeping track of your inventory and can’t access the data in real-time, you will fall behind. Customers won’t throw you off when a request or priority order is made, helping improve the service you provide and ensure you prevent inaudibility, frustrations and extra costs.
Efficiency Is Key
Cycle Counting allows you to regularly plan inventory counts, helping ensure the physical stock in your warehouse aligns with the data in your WMS and is up to date & error-free. This results with a minimal amount of time being lost on recounting inventory and increasing your warehouse efficiency. As your inventory has already been checked and is always up to date, you eliminate the need for an annual inventory check of the entire warehouse – saving you and your employees precious time, effort and money.
Your wish is our command
Start working proactively for your customers and instantly provide them with the latest inventory status whenever they request information. Furthermore, a distinction can be made between fast and slow-moving goods. It is possible to design the module in such a way that A is counted weekly, B is counted monthly, and C is counted annually. You can even have a different setup per customer. For example, the stock of customer X is counted weekly while customer Y decides a monthly update is enough. In this way, it is possible to anticipate better on customer requests.
Always stay aware
Besides raising the efficiency and improving your service level, another advantage is that your order pickers never run out of stock again. By using Cycle Counting you minimize the number of differences between your system and the actual inventory. When Cycle Counting isn’t used, the remaining stock would be incorrect and your employees would be required to count the remaining products before continuing the process. As you can see, Cycle Counting keeps you and your employees from surprises and speeds up the handling to save time, energy and money.
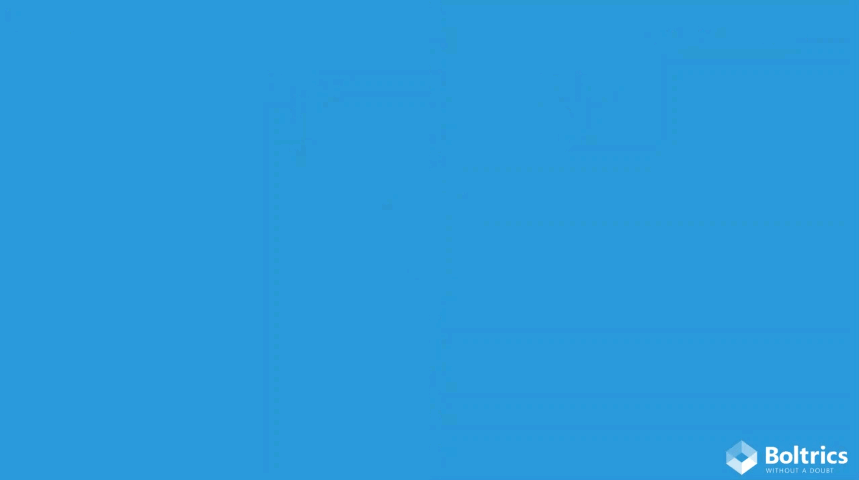
Interested in Cycle Counting but no clue where to start? Or would you need help by implementing the module in your own warehouse?
Contact us today to request a demo or find out any more information.
Further reading
Adjust carriers for shipments based on delivery conditions
During implementation, our consultants often get asked whether 3PL Dynamics can handle customer demands for delivering the goods you ship from your warehouse. For example, consider specific carrier types or maximum heights your customers use. In that case, you want...
Print labels quicker, safer, and more flexible with the new Transsmart API
Printing labels. Finding the best courier. Checking the latest order status. These activities may seem a small part of your logistic process but especially these have a huge impact on the efficiency of your operation. Therefore, 3PL Dynamics integrates with Transsmart...
Private hardware vs. cloud-based software: the shift to SaaS
Technology is of great importance for your logistics operation. A strong software system helps you to be successful. However, the time that you run self-developed software on your local servers is past us. Way past us. Software suppliers massively switch to the cloud....